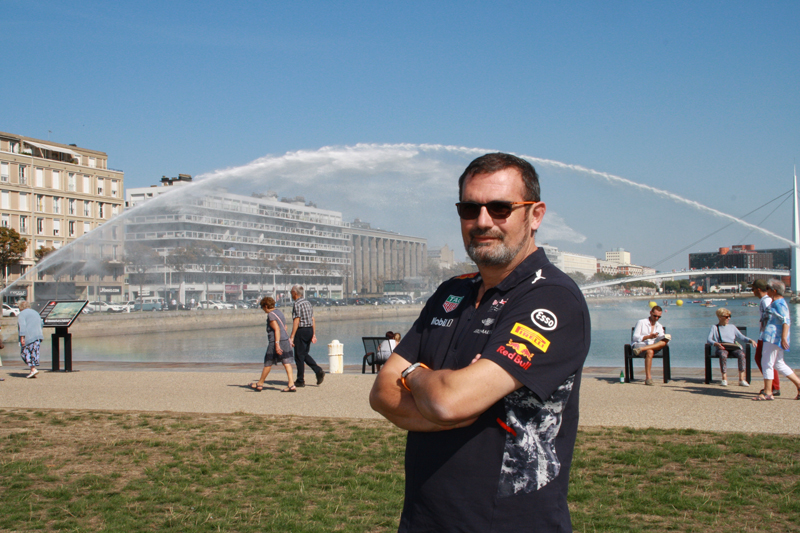
Matter to… put in motion
His collaboration with Crystal Group has been going on for almost twelve years. He moves our mechanical arms, all our jets and water effects, lighting… In short, everything that moves, he moves it. Discover the journey of this enthusiast who made the leap from the world of industry into events.
What is your role at Crystal Group?
I am responsible for automation at Crystal Group. For the majority of our projects, I work with everything concerning fountains and, in particular, multimedia shows. Of course, I also sometimes work on decoration and ice. I also build all our technical cabinets, with the help of my team.
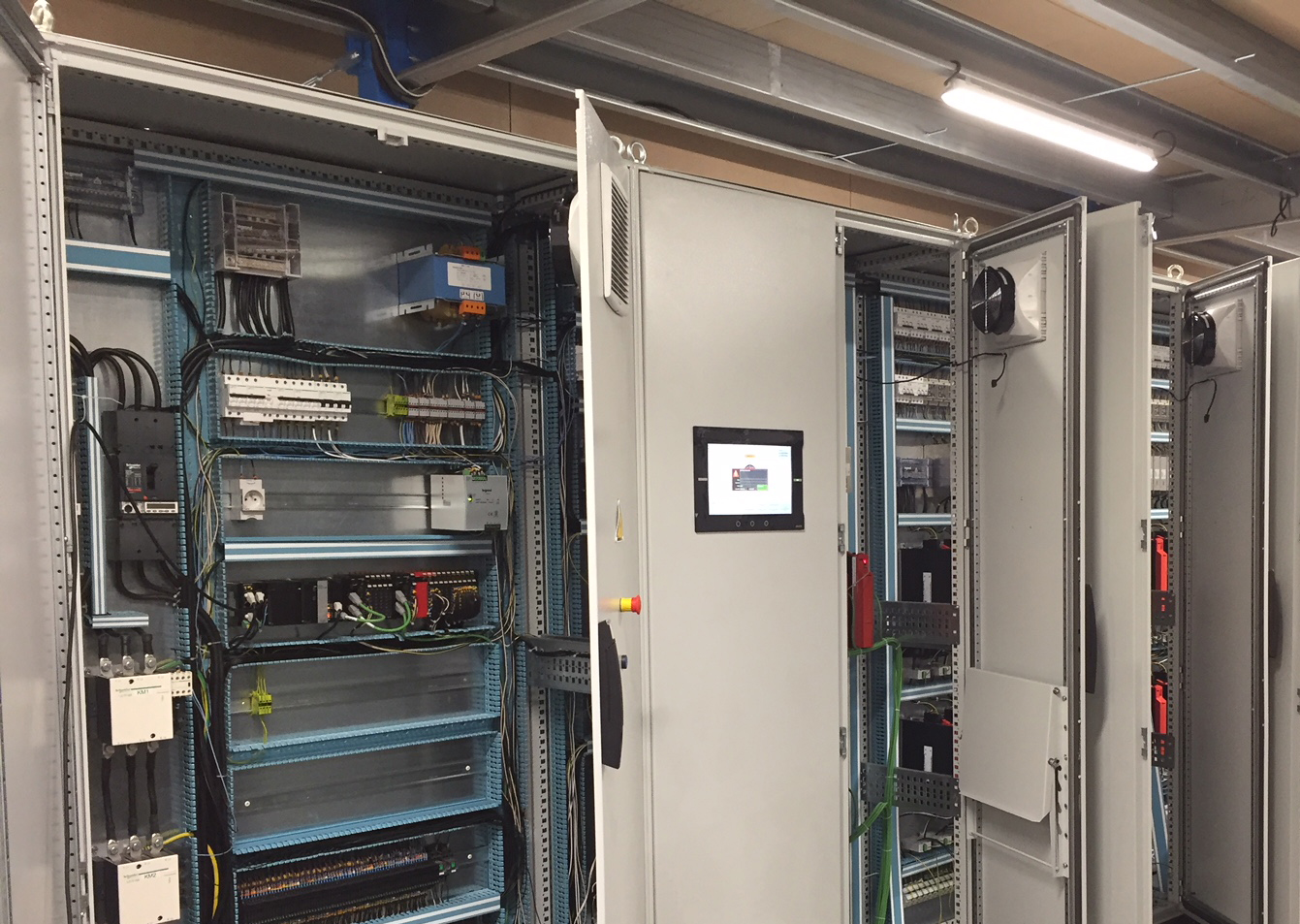
What is your background?
I studied a baccalaureate and advanced technician’s certificate in industrial automation. I started my career in 1989 in a company that specialised in making machines for automobile factories, in particular for assembly lines.
In 2002, I created my own industrial automation company, which was also focused on the automobile sector.
It was in 2006 that I started working with Crystal Group on a brand new project: the pixel fall. I had to design this product, which at the time was still very new, and which proved very complex to programme, especially given the level of satisfactory image quality that had to be reached.
In fact, the study and development of this project lasted almost two years. Meanwhile, other automation projects cropped up and my company joined the group in 2008.
Le passage de l’industrie à l’événementiel s’est bien passé ?
It is certainly true that I was completely unfamiliar with this sector. I had only worked on car production lines. I remember that our first pixel fall was installed at a Peugeot stand at an event in Germany!
From a technical point of view, we had to bridge the gap between the automaton used for industry and that used to manage our shows. We have created an app that is capable of understanding and communicating an event-specific programming language (ARTNET).
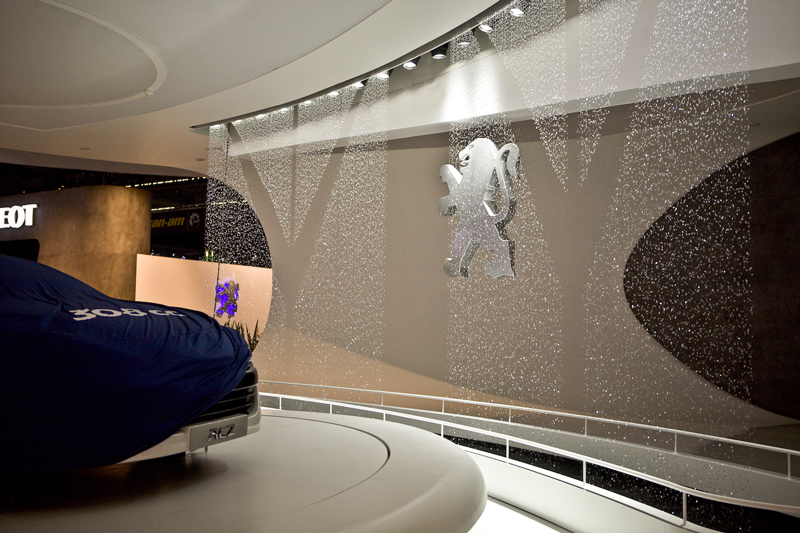
What do you like best about your job?
It is a job in which you always have to be on the lookout for innovations. The sector is ultimately based on computer science and, of course, this field evolves very quickly. Systems are becoming increasingly sophisticated. Today, for example, everything is networked which enables better data fluidity. And I’m not talking about the evolution between digital and analogue!
These technical innovations force us to continually question ourselves. We progress and learn with every project. This constant reassessment requires regular training and privileged relationships with manufacturers, who keep us informed of their innovations, new processes and equipment.
In our automation department, development represents at least 30% of our activities and budget.
In addition, it is important to always stay one step ahead of the demands of the design office. We have to be able to ascertain very quickly whether we are able to do something or not. Always with the knowledge that such an artistic director as Michel Amann* regularly pushes us to surpass ourselves! Today, I cannot recall a project that we were incapable of completing from a technical point of view.
Can you explain more concretely what automation is?
It is the management of all electrical, pneumatic and hydraulic systems. The goal is to set in motion the jets of water, mechanical arms and all kinds of aquatic systems that we use, in accordance with the information we have been provided with. This might involve putting in motion a carriage on a rail, like the one we created for Eurodisney, a mechanical arm or a car that has to drive across 100 metres of water for the Futuroscope show. In our automation department, there are five full-time staff.
Of course, we work on several projects at the same time. We usually carry out three or four projects simultaneously. In addition to this, we have to keep up the maintenance work of our permanent installations, which are located across the world.
This area of automation allows me to feel as though I am at the heart of the project. Systems would not work without automation. We create the brains of the shows and spectacles.
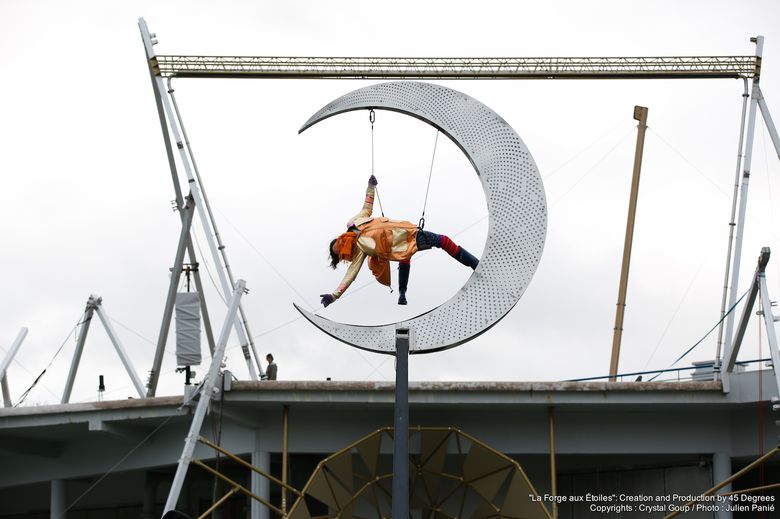
When you talk about brains, are you talking about those large cabinets that contain the automaton?
Exactly. When creating an electrical cabinet, we start from scratch. Every cabinet is its own creation. They are utterly logical creations since every cabinets must be precise and tidy. Every component must be in the right place and every wire has its own specific colour and number. For me, when it meets all these criteria, a cabinet is a thing of beauty. And yes, even an electrical cabinet can be beautiful! That is definitely where my ‘little’ artist side lies!
Could you tell us about some of the projects that you are particularly proud of?
It has to be the pixel fall, which remains the first project I worked on in collaboration with Crystal Group!
I would also say the Futuroscope show, ‘La Forge aux Étoiles’. This is one of the largest installations we have ever worked on. Between the mechanical arm, the car, the water, light and mist effects, we can feel very proud of this multimedia show. We created everything.
I also enjoy working on all our installations in China, both in terms of scale and technicality. In fact, the more I work, the more it fascinates me!
These projects allow us to work with some amazing companies. We can only achieve high-end results. Working with the biggest names constitutes true recognition.
*Michel Amann, Associate Director.